在化学工程的设备制造安装中,钛及钛合金的应用越来越多。但由于在焊接施工中受地区、季节、保护条件等环境的不利影响,常易出现质量问题。在众多的焊接缺陷中,焊接裂纹危害性最大,且占一定的比重(返修难度亦较大)。由于有些设备需运到施工现场进行组对焊接,它的焊缝相对较多,焊缝集中,加之卷制与现场组对焊接产生的多向应力,致使焊缝的裂纹问题甚为突出,施工环境越差(尤其在东北的冬季和湿度较大的沿海地区),钢板的强度越高厚度越大焊接裂纹的敏感性越强。下面结合近几年来现场焊前试验及工程实践,就工业纯钛设备焊接裂纹的种类(又发现了新裂纹)、形成机理及质量控制问题予以研究。

1、焊接裂纹及其机理研究
1.1钛材的主要物理化学性能分析
工业纯钛根据其杂质(主要是O2和Fe)的含量以及由此而引起的强度差,分为TA1、TA2、TA3三个牌号,通常它们具有良好的耐蚀性、塑性、韧性、焊接性和较高的比强度,主要用作化学工业之中的耐腐蚀结构,如设备、容器、管道等。
工业纯钛的熔点高达1672℃,在常温下,由于钛表面致密氧化膜的作用,使其性能很稳定。但钛在高温下具有很强的化学活泼性,随着温度的升高,其化学活泼性会迅速增强。高温钛有强烈的吸收空气中氢、氧、氮的能力。空气中固态钛在250~300℃开始吸H2,在400℃时开始吸O2,在600℃时开始吸N2,同时,焊接中当温度达到400℃以上时,除了H2、O2、N2以外,还和其它一些诸如C、Fe、Si等杂质元素发生反应,从而降低了焊接接头的塑性和韧性,其强度大大增加,脆性亦相应增加。此外,O2、N2都是稳定化学元素,当其含量较少的时候,都会作为间隙元素固溶在钛中,这也是降低钛材塑性,导致产生焊接裂纹的根本原因之一。
1.2常见焊接裂纹俞与原因
工业纯钛化学性能活泼,固态加热到400℃以上高温时,很容易被油脂、水分和空气污染,由表面层剧烈吸收C、H2、O2、N2等杂质元素,致使焊接接头的韧性和塑性下降而导致性能转变,由原来的初始状态向高强、脆化转变,高强、脆化对焊接接头的质量均有明显的不利影响。
工业纯钛的熔点高,导热性差,热容量小,导温系数低,电阻系数大,所以在焊接时熔池内积累的热量多,不易散发,熔池温度停留时间长,冷却速度慢,焊缝容易发生过热现象,出现过
热的组织,使晶粒变得粗大,晶粒尺寸加倍长大,在冷却收缩过程中,由于拉应力的作用,再加上前面分析过的低塑脆化原因,很容易引起焊缝产生裂纹。尤其是在冬季、湿度较大的东北沿海地区焊接大型结构和容器时,产生裂纹的比率大得多。
在常规情况下,裂纹大致可分为两种形式,即热裂纹和冷裂纹。由于工业纯钛高温强度大,塑性好,凝固时收缩量小,在结晶时晶面上形成的低熔点共晶杂质少,结晶时温度不易散发,温度区间小,所以在一般的情况下不易产生热裂纹。然而由于氢从固溶体析出TiH2的作用,使金属脆化并引起很大的组织应力,再加上焊接残余应力的作用,材料本身的塑性已经降
低、脆性增加,很有可能在焊后产生冷裂纹。
1.3弧波裂纹及其形成机理探究
高温波动及其裂纹催生。在此暂称它为弧波裂纹,它不属于金属常见焊接裂纹,如热裂纹、冷裂纹、再热裂纹与层状撕裂裂纹等类型范畴,也有别于常说的热疲劳裂纹(外在要素明显,多针对铸造模型)。即焊缝处经过反复多次急速地加热与冷却后而形成的一种裂纹,其发展趋势最终为断裂。它多发生在:厚壁设备及管道的多层多道焊焊缝区域上(主要在熔合区附近)或焊缝修补之处。特征是:裂纹区域材质性能发生变化(尤其是塑性、韧性降低),晶粒松弛,晶格歪扭,有局部硬化现象。有时裂纹旁边伴有若干更细微裂纹。它发生的滞后性强,其隐蔽性危害性比其他裂纹更大。目前形成机理仍在研究之中。笔者认为,从本质上看,钛材焊缝处多次反复加热与冷却,一是应力不断扩张、收缩,致使焊缝疲劳开裂;二是加热过程中晶粒不断长大(有时连续有时断续,但多为波段式变化),从而使显著长大的粗化晶粒间松弛、脆弱;加之焊缝处若干次地快速冷却,化合物逐渐析出、积聚、延伸,出现薄弱边缘而致裂。因此,给焊接操作者提出了更高的要求,焊接时,在保证焊缝金属晶粒度细小及应力勿过大或集中的前提下,尽可能采用较少的焊接层数及弧焊波动(此点过去往往被忽略)。此类裂纹是若干因素(最高加热温度、加热与冷却速度、高温停留时间、焊弧波动的幅度及次数等)综合作用的结果。消除和减弱其中的任何不利因素,对于防止它的产生都是有利的。
根据长时间的试验数据统计和近期研究结果,发现多数金属材料焊接层数(弧波次数)与焊接裂纹有一定的内在联系,如表1所示。由此可见,不同材料根据自身特性均有一个最佳
焊接层数的问题,即焊接裂纹倾向最小时的适宜焊接层数。钛材亦如此,这要根据不同材质的牌号,当时的具体施工条件由焊前试验来确定。
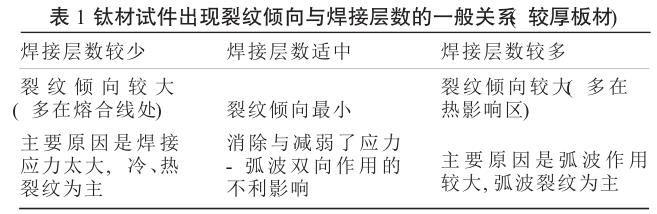
近年来的研究结果还显示,虽然有时钛设备某焊口经无损检验未发现任何缺陷(达到合格水平),但在随后的施工或设备运行过程中,由于焊缝薄弱处已达到开裂的临界或近临界状
态,,一旦遇到较恶劣的环境和波动的工况,随即开裂。因此,焊接时除了要保证焊缝短期达标外,还应尽可能使焊缝的薄弱区远离危险的开裂临界区。
2、若干优化工艺措施
2.1焊前准备和焊接材料的选择
焊接方法的选择,根据纯钛的物理、化学性能和特点,现场多采用TIG焊接。焊丝的正确选择是保证纯钛焊接质量的关键。为了保证焊缝与母材等强,原则上采用与母材化学成分
相同的纯钛材料,一般要求焊丝中有害杂质越少越好,在焊丝与母材不匹配的情况下,也可以从母材上切取的方法来解决。
氩气的纯度将直接影响到纯钛焊缝的硬度和韧性,对焊接裂纹的产生也有着明显影响。氩气的纯度低,其杂质的成分就多,尤其H2的含量,如果含H2在0.001mL/L以上,相对湿
度大于5.0%,露点在-40℃以上,就容易在焊缝中引起脆化,产生裂纹。所以,要求纯钛焊接用的氩气必须是高纯度氩(富氩Ar99.99%),露点在-40℃以下,H2O小于0.001mL/L。
2.2几项主要焊接工艺及技术措施
2.2.1焊接设备及其辅助设备
钛设备施焊前应按有关规范及规程要求进行焊接工艺评定。然后根据此焊接工艺评定在正式施焊前组织参加焊接的焊
工进行适应性试验,以保证正式焊接中获得较好的质量。此外,需做好以下几方面事情。选用适宜的钨极氩弧焊机(最好是逆
变电源),焊机带高频或高压起弧装置,施焊中严禁采用擦弧引燃的方法。选用精确的氩气流量计以控制气流量。送气软管选用塑料管,不宜采用橡胶管输送氩气。保护罩的材质选用奥氏体不锈钢或铝、铜,不得使用碳钢。所用清理工具只能用于钛,不得混用,在使用前应清洗干净。
2.2.2焊接层数及其确定
在中、厚壁钛设备的焊接中,应采用多层焊,但根据多年试验和经验表明,层数过多易带来负面影响,主要是焊缝区受
到焊接热循环作用次数过多易导致性能劣化、引发弧波裂纹。事实是,在保证材料晶粒度细小及应力较小的前提下,尽可能
地减少焊接层数。对于工业纯钛设备,一般按下式选取焊接层数:n=S/md(式中,d为焊丝直径,mm;S为设备壁厚,mm,根据经验修正系数m通常取0.8~1.2))。此外,设备壁厚不同,焊道亦不相同,实际操作中,设备焊缝的焊道数量通常按表2予以选取。

2.2.3坡口加工与清理
坡口切割与清洗工序必不可少,钛板切割可用机械方法进行,在切割过程中,不得使其过热而变色,在坡口内外表面不
小于20mm范围内用砂轮和不锈钢丝刷打磨出金属光泽,然后用刮刀修整坡口的毛刺和钝边,之后再打磨光滑,避免在清
洗的时候挂丝。清洗质量的好坏会直接影响到焊接裂纹的产生,清洗质量不好时,会在母材及焊丝表面上生成一层灰白色
的吸气层,导致焊接裂纹和气孔的产生,因此清洗时要注意以下几点:
①先采用酸洗。酸洗液为2%~4%HF+30%~40%HNO3+H2O(余量)。最后用清水冲洗干净并吹干,临焊前用丙酮或酒精擦洗。②焊丝在酸洗后一般需要进行脱氢处理,焊前再用丙酮脱脂。③严禁使用氧化物脱脂。④清洗时不得戴橡皮手套,以免橡皮和脱脂溶剂发生反应使焊缝产生气孔。⑤清洗后的焊口必须马上焊完,不宜久放(一般不得超过4h),否则需要按前面步骤重新清洗。
2.2.4焊接工艺参数的确定
纯钛焊接工艺的选择,既要防止焊缝在电弧热的作用下产生粗晶组织,又要避免在焊后冷却时被大气的污染出现脆化组织,所以对施工环境、焊接区域内的保护至关重要。与不锈钢设备相比较,除了与不锈钢焊接保护有相似的地方外,还必须对400℃以上的区域用托罩进行保护,因为钛在400℃以上的高温区,化学性能特别活波,很容易吸收有害气体,导致材料性能降低出现裂纹。
对于小型设备,可在设备内充氩保护。焊接时,必须自始至终地充氩保护,直到温度降至材质稳定的范围。这是焊接钛
材的关键要领。考虑保护效果,焊接时尽量采用大直径的喷嘴,喷嘴与焊口距离适当缩小以加强保护,钨极伸出长度宜短,以
不妨碍视线看到熔池为限。氩气流量大小对保护有着相当的影响,过大的流量不容易形成稳定的气流层,反而在保护区内形
成紊流,使有害气体浸入熔池。另外,过大的气流使得熔池冷却速度加快,焊缝表面容易出现裂纹。过小的气流使保护不到位,达不到保护效果,所以保护气的流量一定要适中。在焊接时,拖罩和喷嘴的距离始终保持在20~25mm范围内,
当焊接结束时,拖罩保护不能立即结束,必须等焊缝温度降至200℃以下才能停止送气。
纯钛设备的TIG焊基本上与不锈钢焊接相同,为了克服热影响区温度的提高,在保证完全焊透的情况下,尽量采用较小焊接线能量的操作方法,即快速焊、直线运把和填充焊丝(电流太小容易产生气孔)。除此之外,焊接过程中还必须注意如下事项:①焊前预先通氩气一段时间进行置换,可采用明火检测法对焊口进行检查,确认设备内气体完全是氩气了,然后再进行焊接。②采用短弧焊,不摆动焊把和焊丝。盖面时即使要摆动,也只能是微幅慢速摆动。③焊丝端部在焊接过程中不能脱离保护范围,否则焊丝端部会被氧化,如发现焊丝端部已经氧化,须将氧化部分切去然后才能使用。④焊接时,起弧和收弧点
必须是在坡口内进行,不得在母材上起弧和收弧。送丝的时候不能将焊丝快速地一送一抽式移动,应当慢速均匀地将焊丝往熔池里面填,否则会造成气体紊乱,影响保护效果。⑤焊接时,喷嘴和焊件角度为70°~80°,焊丝与焊口的夹角为10°~15°。⑥在焊接过程中,必须严格控制层间温度,每焊完一层定要等温度降至室温时再继续下一层的焊接。表3为几种壁厚设备的焊接工艺参数(TIG、供参考)。
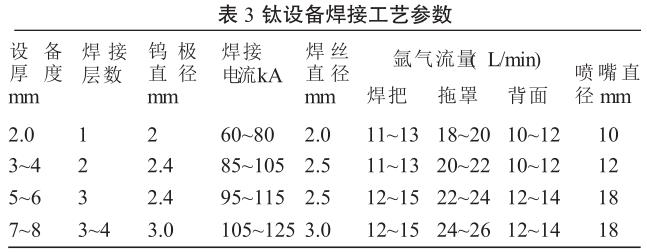
2.2.5操作技术要点
焊接时要时常观测焊缝表面颜色,以银白色为最佳,其次是金黄色。否则要调整焊接工艺参数和保护气体流量。对焊接
环境的要求。按纯钛的焊接要求,焊接施工现场必须保持干燥、清洁、焊接时的环境温度应控制在10℃以上,焊接区域没有过堂风,焊接熔池和热影响区绝对禁止水或水气及其它气体的渗入,如遇有上述情况,一定要有遮挡、保温、除湿等措施,避免焊缝受到污染产生裂纹。
2.3氩气保护效果判别及其裂纹等缺陷的返修
在施工检查中,如发现焊缝保护不佳,应停止焊接。如产生了焊接裂纹,亦应即刻返修,以免裂纹延伸,返修裂纹要注意
如下事项:①用着色的方法检查出裂纹和两头的终端,用合金钻头在终端处打出止裂孔,将裂纹及其两侧用聚酯磨光片打
磨,清除裂纹和两侧表面氧化层。打磨时要有间断性,以免局部区域温度升高而导致母材再次被污染。②再用着色法检查,确认裂纹彻底清除干净后,进行对止裂孔和打磨处的清洗。③焊接方法和工艺参数与正常焊接相同。但是,在修补裂纹时,切不可忽视了在焊缝正、反面再次充气保护。④补焊时一定要控制层间温度,每层焊完都必须进行必要的着色检查和清洗工作。
3、其它注意事项
①焊后处理及检验。钛设备焊后都需对焊缝及热影响区进行酸洗,然后用清水将酸洗液清洗干净。焊后检查主要有如
下几项:外观检查,焊缝表面无咬边、焊瘤、气孔、夹渣、裂纹。色别检查,焊口表面呈银白色的占80%以上,其余为金黄色,证明焊缝保护效果良好。X射线检查,应无裂纹和未焊透以及超标的气孔、夹渣等缺陷。②根据钛材的焊接特性,凡是在焊接过程中能有效地防止气体污染的焊接方法均能采用,如钨极氩弧焊、熔化极氩弧焊、等离子弧焊等,但根据现场的施工条件,采用钨极氩弧焊(直流正极法),既能保证焊接质量,又能适合现场条件下的各种位置焊接。③焊丝选用与母材化学成分相同的材料,并附有质保书(有时为了提高塑性也可选用比母材合金成分低的焊丝),决不允许有裂纹、夹层等各种内在及表面缺陷,并且焊前予以彻底清理。钛设备对接焊缝通常采用V型单面60°坡口,1~1.5mm钝边,对口间隙2~2.5mm。④对大、中型设备,可采用槽内充氩保护焊缝及近缝区的内表面,槽内亦应提前送气排净空气,并保持微弱的正压和流动状态,而后起弧焊接。尽可能选用较小线能量以减少金属过热和氢的溶入,保证焊缝质量。⑤焊接过程中应保持稳定,防止钨极与焊件或焊丝接触造成夹钨,当出现夹钨时,应消除缺陷后方可继续施焊。若采用多层焊,层间温度控制在200℃以下,脱离保护罩温度控制在400℃以下。⑥此外,设备在组对纵、环焊缝时,要保持内壁平齐,错变量不得超过壁厚的10%。要严格控制焊后的冷却速度在适宜的范围,通常为10~200℃/s。焊接时如发现蓝色和灰白色,必须磨掉(磨光机应在低速下使用,以防高速时金属着火氧化),重新焊接。
4、结语
在某化学工程通过对三台钛设备现场安装、焊接中,所用技术措施对钛设备焊接裂纹的控制方面起到了积极作用,有效
地控制了在焊接过程中裂纹的产生,并成功地修补了二处裂纹,经着色检查后全部为合格,其效果令人满意。
归纳起来钛设备现场的焊接过程,关键的几个要点必须控制好,即打磨———清洗———环境———保护——
—参数———焊接———后处理,这些节点每一个都很重要,缺一不可,必须认真对待。实践证明,只要严格按照规定和适宜的工艺参数进行施工,就能制造焊接出满意合格的产品。
参考文献
[1]朱方鸣.化工机械制造技术[M].北京:化学工业出版社,2005.
[2]张麦秋.化工机械安装修理[M].北京:化学工业出版社,2004.
[3]刘云龙.焊工技师手册[M].北京:机械工业出版社,2000.
[4]邹广华,刘强.过程装备制造与检测[M].北京:化学工业出版社,2003.
[5]魏康民.机械制造技术[M].北京:机械工业出版社,2002.
[6]阮鑫钛材焊接缺陷分析与焊接质量控制〔J〕.机械工程材料2004,28(8):52-54.
[7]康浩方.国外钛设备的焊接技术现状[J].钛工业进展,2003,20(4-5):70-72.
[8]中国机械工程学会焊接学会.焊接手册〔M〕.北京:机械工业出版社,2001.
[9]曾乐.现代焊接技术手册[M].上海:上海科学技术出版社,1993.
[10]冯兴奎.过程设备焊接[M].北京:化学工业出版社,2003.
相关链接