钛材越来越广泛用于化工医药等行业的机械设备制造和安装行业。钛材特点是密度小、强度高在海水和大多数酸、碱、盐介质中均具有优良的耐腐蚀性。在尿素、硝酸、农药等生产中其抗腐蚀性远高于超低碳奥氏体不锈钢。大量用于化工过程设备。但由于钛的焊接变形大校形困难;钛在冷加工时易产生裂纹;其冷作硬化倾向的强化程度随变形速度而加剧;变形速度对加工零件的极限程度和质量都有很大影响。更不利的是钛制设备不容易返修好有时会产生愈返修效果愈差的情况。针对钛的这些特性钛储罐、钛反应釜、钛换热器等钛设备在施焊过程中需要采取一些特殊工艺措施和技术手段才能保证焊接质量。
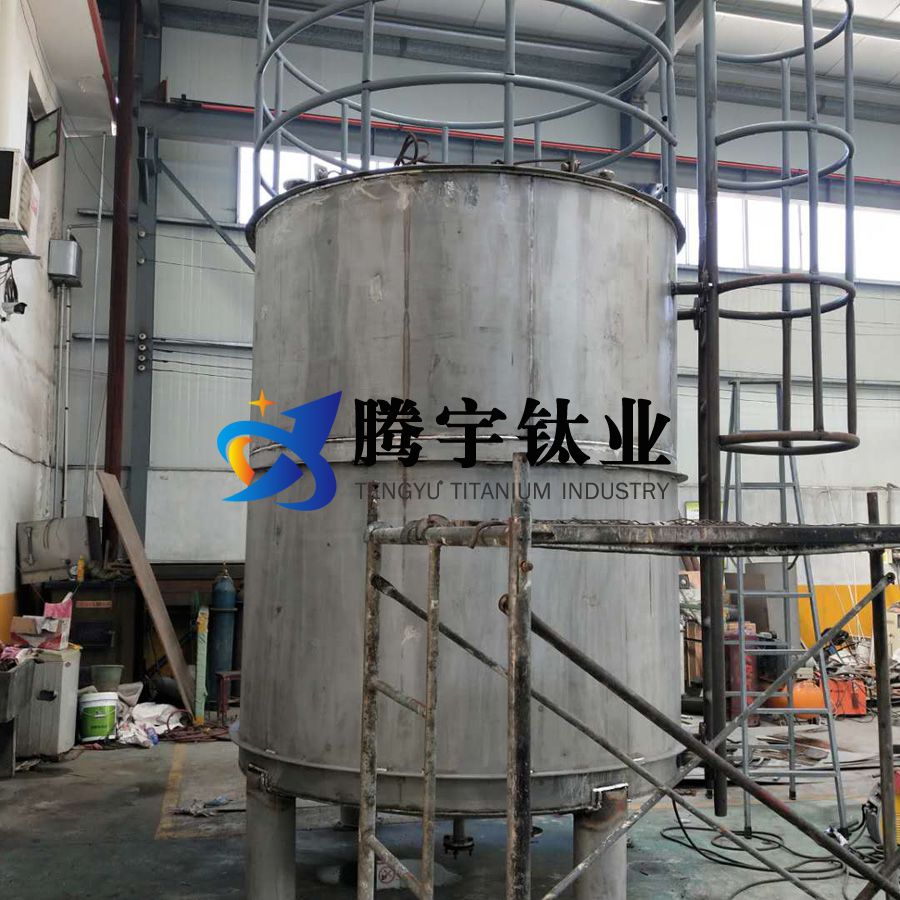
1 、钛材特性
设备常用钛材按生产成型的方式不同可分为压力加工钛材、铸材及粉末冶金钛等。其中压力加工钛材是化工设备用钛中用量最多的类型。设备用钛要求有更优越的塑性和焊接性能钛材中杂质含量会严重影响焊缝质量含氢会使钛材产生氢脆现象并产生腐蚀针孔;钛中氧含量增高会导致气孔;钛中含铁量过高容易在焊缝附近出现稳定的富铁相区与钛基形成腐蚀电池使钛发生电化腐蚀等。因此设备用钛选用杂质含量较低的工业纯钛和低合金钛牌 号如常用的有TA0、TA1、TA2、TA3、TA9、TA10等它们具有良好的耐蚀性、塑性、韧性主要用于化工设备的耐蚀结构材料。表 1是钛材在几种介质中的耐腐蚀情况。
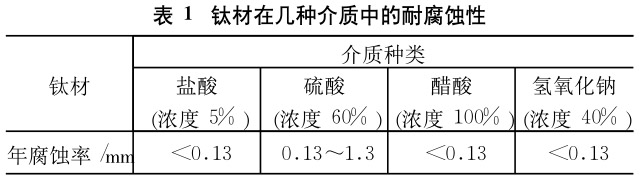
2、 常见焊接缺陷分析
(1) 烧穿。烧穿多发生在薄板焊接。其原因是:装配间隙过大难以承托熔化金属;背面保护气流过大而冲破熔融金属;电流过大焊速过慢;焊缝外有灰尘或杂物焊接过程中引起爆炸冲掉熔池金属液。
(2) 断裂。引起钛材焊缝断裂的因素相当复杂但最主要的是氢、氧、氮等杂质的污染。焊缝吸氢量超过室温下的固溶度同时又受氧、氮等污染严重时就会出现氢脆断裂。该断裂有的是在运输或使用过程出现也有的是在焊后放置一段时间后出现。如某企业曾焊接一个材质为工业纯钛的二氧化碳汽提塔焊后质检合格但放置一段时间后焊缝出现裂纹。防止钛焊缝断裂除采取适当焊接措施及加入合金元素来增大氢的固溶度外最主要是防止吸氢及氧、氮的污染因此焊前清理及焊接过程中进行保护极为重要。
(3) 气孔。气孔有内、外两种。外气孔通常产生于焊缝表面;内气孔通常产生在熔合线附近。一般来说氢和氧及表面上存在的吸附水分和气体是形成气孔的一些因素。其来源主要有:母材及焊丝中氢氧含量过高坡口过小而焊时熔质过多这主要形成内气孔;焊接时保护不善大量吸气;表面清理不净有油脂及其他有机物污染;保护气体纯度不高湿度过大。
(4) 焊缝腐蚀。受铁污染严重时焊缝会出现稳定的富铁相区与铁基形成腐蚀电池而发生电化腐蚀。所以机加工后的坡口必须经酸洗才能施焊。此外气孔也会引起针孔腐蚀。
除以上焊接缺陷外笔者在多次对钛设备焊接试验和焊接制作实践中发现一种新的裂纹即焊缝处经过多次反复加热、冷却形成的裂纹暂称为焊接循环温变裂纹。
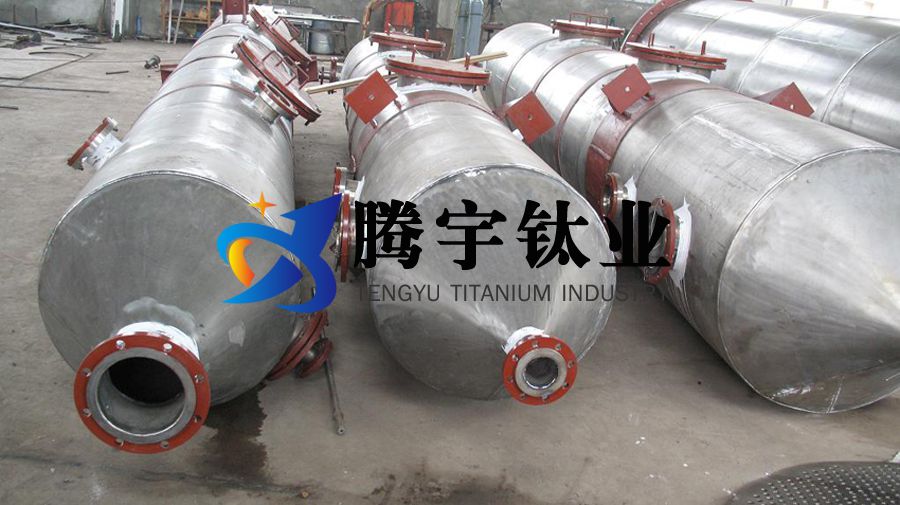
它多发生在厚板的多层多道焊缝区域。特征是:裂纹区材质塑性、韧性降低晶粒松弛晶格歪扭有局部硬化现象。有时裂纹旁伴有更微细裂纹。它发生的滞后性强其隐蔽性危害性比延迟冷裂纹更大。笔者认为由于钛材焊缝处多次反复加热与冷却应力不断扩张、收缩致使焊缝疲劳开裂;再者加热过程晶粒不断长大使粗化晶粒间松弛、脆弱出现裂纹等。因此从焊接工艺角度看适当控制焊接最高加热温度、加热速度、高温停留时间和冷却速度及尽量减少焊缝区的加热与冷却频率和次数是必须要注意的问题。
3、 钛设备焊接工艺的优化
3∙1焊接方法的选用
钛和钛合金的焊接方法主要有惰性气体保护电弧焊、等离子焊、电子束焊等。一般情况采用惰性气体保护焊通常是氩气保护焊。为获得优质焊缝对焊接熔池及400℃以上的热影响区都必须采取保护措施以免受空气中的气体污染。对大型工件及薄板 (3~12mm) 的焊接应采用等离子焊等离子焊速度快、焊缝窄、焊接热影响区小且由于钨极缩于喷嘴内焊缝可避免钨污染焊缝成型美观。但由于其线能量大需加强焊接区的保护及冷却效果。而对于小型、重要零件的焊接则应选用电子束焊并且必须在真空箱中进行。
3∙2焊丝
钛设备要求焊后状态的焊接接头的强度不低于钛材母材标准的下限伸长率不低于或至少接近于钛材母材标准的下限所以容器用钛焊丝要求更低的杂质含量才能使焊接接头达到足够的塑性要求。容器用钛焊丝应按JB4745-2000 “钛制焊接容器 ” 中规定的容器用钛焊丝见表 2。
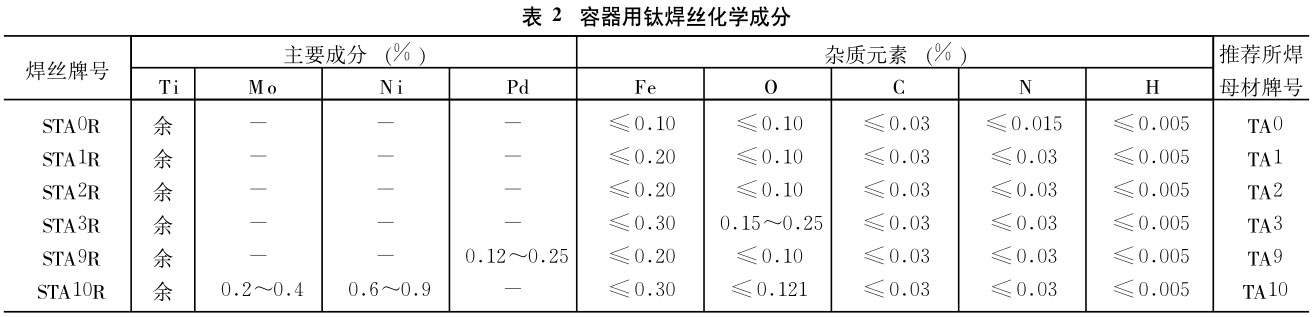
一般来说根据母材牌号选用相应牌号的焊丝。对于容器用钛焊丝要求通过规定的焊接工艺评定。另外由于焊缝强度与塑性受其他焊接工艺的影响有可能采用相应牌号的焊丝不一定能与母材有最好的匹配这时可选用纯度高一级或低一级的工业纯钛焊丝:如焊缝强度偏高太多可改用纯度高一级的焊丝;如焊缝强度偏低可改用纯度低一级的焊丝。焊丝的选用仍根据焊接工艺评定结果来确定。
3∙3焊接工艺优化
(1) 焊接前的准备。钛制设备在焊前的准备工作极为重要尤其是在焊接过程中焊缝的污染和热影响问题。焊缝只要受到小量的有害杂质的污染就会严重影响焊缝的质量影响设备使用甚至报废。所以钛和钛合金在焊接前必须进行严格的清理并在焊接过程中采取有效措施防止有害杂质的污染。焊接前的准备工作包括下料、开坡口、除氢、表面清理、工件装夹。每道工序都要对焊件表面进行清理。采用惰性气体保护焊时厚度为 3㎜以下钛板不开坡口3㎜以上必须开坡口。并应选刨、铣、磨等机加工方法加工坡口严格控制尺寸。
由于氢含量过高会使焊缝产生气孔、微裂纹、氢脆等现象因此必须在真空炉中进行除氢处理使氢含量降低到 0∙002%以下。并在焊前对钛板的焊边及焊丝表面进行除油脂、清除氧化皮及吸气层处理。表面彻底清理完毕即可进行工件装夹。在装夹过程中操作人员必须带清洁手套不要触摸焊口和焊口附近。严禁用铁器敲打焊口以免焊口受铁污染引起焊缝脆化及降低耐蚀性。工件装夹好后还必须对焊口进行一次检查油污或棉纱毛等物都要清除干净才能施焊。
(2) 焊接工艺的优化。为保证焊缝得到良好的力学性能除了对钛材及焊丝成分的纯度要求不低于所规定的成分外对保护气体及溶剂成分的纯度还要提出特殊要求。氩气的纯度不低于 99∙99%即杂质 O2 含量 <0∙003%N2含量 <0∙01%湿度 <0∙03g/m3。焊接过程中要选择正确的焊接规程并在保证焊缝成型良好的前提下采用较小电流和较快速度进行焊接以防止热影响区过大。对于手工氩弧焊为得到良好的保护效果喷嘴应尽量垂直于焊件平面并靠近焊件。焊丝要间断加入熔池填充焊缝但不能把焊丝端头红热部分从喷嘴有效保护区内拿出以免焊丝氧化。焊丝不能在电弧区剧烈摆动否则会破坏喷嘴层流保护区。
(3) 焊接技术措施。① 薄板焊接。薄板容易变形焊接装夹必须采取压板和垫板。压板及垫板可用不锈钢或紫铜。用导热性能好的紫铜时焊出的焊缝性能好。如果所选用的压板为不锈钢垫板为紫铜时在喷嘴处还应加保护罩保护否则焊缝和热影响区就会发生氧化现象。②厚板焊接。钛厚板焊接也可以用铜压板及铜压块以便加速焊缝冷却。由于厚板焊接热影响区宽散热慢需要用较宽和较长的保护拖罩最好拖罩通水冷却。厚板焊接最好采用等离子焊或熔化极电弧焊。采用正极性焊时飞溅小成型较好;用反极性焊时焊丝熔化速度较快适于大坡口的厚板焊接。③ 复合板焊接。由于钛与钢不能直接熔焊所以对钛-钢复合板的焊接可选用间接式焊接接头即钛面、钢面各自焊接复合层间互不熔合。
(4) 氩气保护效果检验与返修。氩气保护方面应加以重视。因钛在 350℃以上会强烈吸氢、脆化引起气孔及裂纹焊接时必须将焊接接头及附近区保护到 200℃为止。每一焊缝要根据行业判定标准进行表面颜色检查(见表 3)。
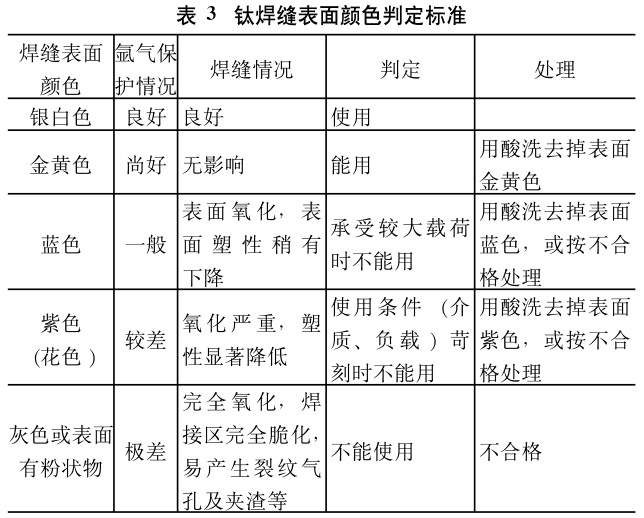
对表面颜色不合格的焊缝和热影响区须用砂轮或风铲全部除去然后重焊。补焊次数最多不能超过两次。补焊位置应在质量证明书上注明。
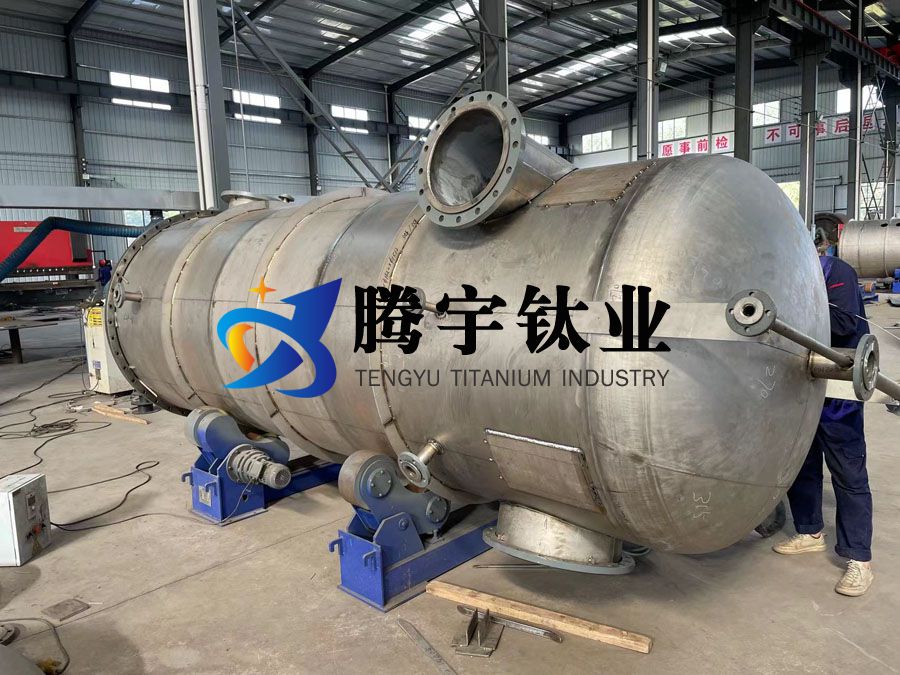
总之在钛设备焊接制作中只要有针对性地采取相应措施严格把好各施焊环节质量关就可取得良好制作效果。
参考文献:
[1] 黄嘉琥应道宴 ∙钛制化工设备[M ] ∙北京:化工出版社2002∙
[2] 冯兴奎 ∙过程设备焊接[M] ∙北京:化工出版社2003∙
[3] 张装生 ∙钛合金焊接工艺的探讨[J] ∙化工装备技术2002 (2):36-37∙
相关链接