1、水冷壁在粉煤气化工艺中的应用
水冷壁的功能是增加燃烧炉的热量回收以及保护燃烧炉的炉体。煤粉气化主要有如下步骤:
第一,原煤磨粉与煤粉除水;
第二,把干燥后的煤粉通过高压输送到气化机中;
第三,燃烧煤粉使煤粉气化,并混合氧气[1];
第四,洗涤合成气体;
第五;处理气化后的残留物。以上过程中气化过程是核心技术,合成的气体中含有大量的氧气与水蒸气,当高压喷头将合成气体喷入燃烧炉内,气体与煤粉颗粒会充分燃烧并释放大量热量,为了防止该热量超过燃烧炉炉体可承受范围值,便在炉内设置了水冷壁[2]。
1)气化炉水循环简图见图1。
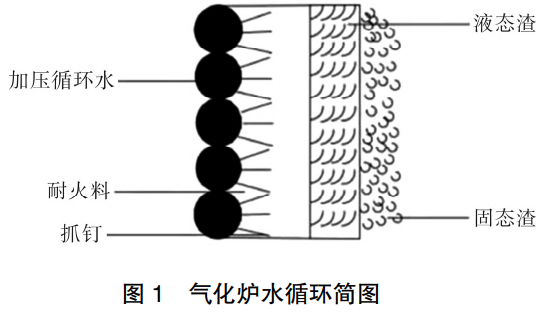
通常水冷壁中有水循环管,管上铺设一层耐火材料并由渣钉固定,其作用是保护水循环管。水循环系统中安装有水循环泵,泵体带动水在循环管中不停地吸收炉内的热量[3]。当循环管中的热量被水吸收后会被运送到中压汽包内,水在其中蒸发后再被送至外界蒸汽网管进行降温处理,随后水蒸气降温后又变为液体进入水循环泵中。
2)当煤粉气化后进入燃烧炉内会形成部分液态水滴与熔渣,而这些液态水滴附着到水冷壁上降温后又会变成固体渣粒,当燃烧周期变长时,水冷壁会被固体渣粒覆盖,且覆盖层会逐渐变厚,随着温度逐渐升高,再次附着在渣粒层上的液滴由于高温环境则不会变为固态渣粒,而是以液态形式附着在固态渣层上形成一层液体层,所以渣层在液态与固态保持平衡的状态下形成一层固液共存的保护层,使水冷壁不受高温烧损[4],水冷壁内部结构简图见图2。
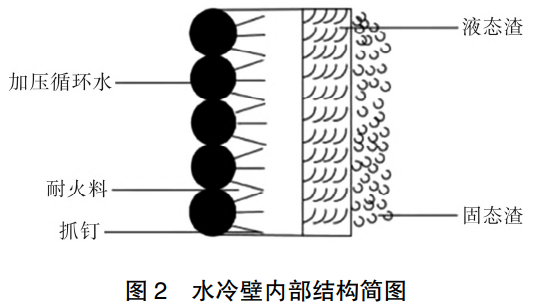
以往的炉内都是耐火砖,当燃烧达到一定周期后耐火砖需要工作人员进行更换维护[5]。由上述可知,固液共存的保护层不仅可以保护水冷壁不受炉内高温的燃烧破损,固体渣层还可以在炉内自动修复,所以水冷壁可减少燃烧炉的维护与停炉环节,更减少了人工成本与材料成本。炉内的循环盘管有三部分组成:烧嘴水循环管、主循环管以及渣口循环管。管内的水循环都有循环泵带动,且每个管都设置了进出口。由于烧嘴循环管承压能力强,所以与水冷壁直接连接且共用一套循环系统。渣口循环管在进口处设置了保护装置,当渣粒流过时可保护进口不受渣粒的冲刷损坏,更能起到缓冲减震作用。
2、水冷壁泄漏现象分析
在对某航天煤粉气化炉进行燃烧研究后发现,该炉内水冷壁出现循环管爆裂、破裂甚至高温熔解现象。通过后期分析,炉内燃烧时环境复杂,水冷壁材料性能下降,具体原因如下:
1)气化燃烧炉内局部温度较高,超过保护层可承受范围。
2)循环管破损导致汽包内液体量减少。
3)汽包压力逐渐降低,与燃烧炉气压逐渐相近。
4)混合气体中氢气含量上升。
5)循环盘管内的冷却水流量变慢,冷却效果减弱。
6)汽包蒸汽量减少,补水量增加,水蒸气散热效果变差。
3、盘管烧损原因分析
3.1水冷壁挂渣和氢裂纹
水冷壁挂渣见图3。
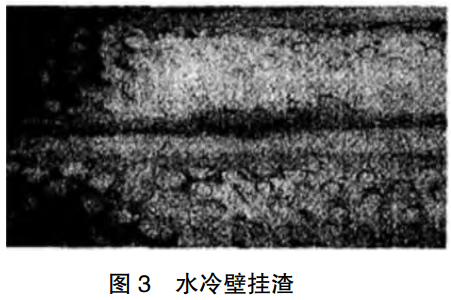
由图3可观察,水冷壁上渣层较少无法形成有效的保护。由于混合气体中氢气含量增加,在高温环境中氢原子含量也随之增加,氢原子在高温环境下会在金属层表面形成结晶。此现象会降低金属表面强度,使金属表面产生裂纹,随后在结晶不断积累情况下会逐步扩大裂纹的范围,形成较大的裂纹,所以水冷壁水循环管出现破裂。据研究,氢气性质活跃,在高温、高压、常温常压下都会影响金属性质[6]。此外,氢对钢的影响是不确定的,有时氢对钢的影响是可恢复的,当氢原子离开钢表面后,钢的性质又可恢复最初状态;而有时氢对钢的影响又是永久的,即使氢原子离开后钢性质会永久受到破坏。
3.1.1在高温高压环境中氨、氮的腐蚀
气化炉中不仅氢气性质活跃,能对水冷壁的盘管造成损害,部分含氮化物与含氨化合物也会对水冷壁的循环管造成腐蚀破坏。其原因是氮与氨在高温环境中在铁离子的催化下会转变为游离态的氮原子,这些游离态的原子会在钢表面形成一层氮化层,特别是温度超过400℃时,该氮化层形成效果明显,此氮化层物理性质硬度较高,且脆性强,很容易使钢表面产生集中应力,当应力值到达一定范围钢表面就会产生裂纹[7]。
3.1.2水冷壁在高温高压条件下的硫腐蚀
气化燃烧炉中含硫的化合物也会对金属造成一定的腐蚀,当炉内温度升高时,硫化物会使金属盘管表面发生应力破坏,使金属局部的应力值增高,此现象不能在早期被发现,当应力值超过金属固有的屈服强度时,金属才开始出现破裂腐蚀现象,所以硫化物造成的危害具有一定的隐蔽性,早期很难发现。通过研究,硫化物引起钢体材料腐蚀破坏的原因如下:
1)硫化物在水与高温的环境下会降低水循环管管壁的韧性与塑性,所以管体材料脆性增强,当整个管体在受到外界影响下极容易发生破裂。
2)当水冷壁盘管的盘管在高温环境或外力作用下,表面会产生平行裂纹,而裂纹再逐步增大就会产生阶梯形裂纹。此外金属表面高温环境中会产生表面气泡,气泡到后期也会产生裂纹,这些裂纹的诱发原因皆是由炉内氢原子,且氢原子的影响超过了硫化物腐蚀的影响。由于气化燃烧炉内水冷壁系统的水循环管渣层较薄或部分区域无渣层,氢离子则会对金属材料表面产生腐蚀性破坏,且后期氢离子离开后金属性质不能恢复到之前状态,裂纹还会逐步扩大,甚至有熔解现象,导致冷却效果减弱或消失[8]。
3.2原料煤影响
水冷壁损坏不仅受混合气体的影响,不同的主煤源也会造成不同的影响。通常主煤的用量是配煤的2倍到5倍,当主煤源用量与类型发生改变时,燃烧产生的热量与燃烧后混合气体成分的含量也大有不同。当调整改变主煤源时,燃烧热量波动也会随之变化,最大波动热量是以往的两倍,最小只有以前的十分之一。所以在这种不稳定的气化炉环境里水冷壁盘管的渣层平衡状态也会发生变化。当气化燃烧炉内的粉尘浓度降低,水蒸气含量增高,盘管上附着的保护层就不能长期形成一个固定的平衡状态,水冷壁就会被高温烧损腐蚀。
3.3煤线煤流量波动影响
1)煤料供给不均匀也会影响水冷壁的冷却效果,例如,煤粉运送的导流管与煤粉输送罐接口处出现泄漏,所以煤粉在运送过程中部分煤粉会在泄漏处流入罐体空腔。当气化炉停止运行时,积累的煤粉就会结成较大的块状煤,等下次再开始工作时较大的块状煤又会进入气化炉中。此时块状煤燃烧的效果与煤粉完全不同,煤线流量出现波动,燃烧的热量也会产生局部升温或降温的现象,若炉内部分区域温度偏高时,会导致该区域水冷壁盘管的保护渣层动态平衡产生破坏,盘管冷却功能减弱或丧失。
2)当煤粉的管线出现磨损时,水冷壁冷却功能会受到一定影响,所以管线处的维护与更换是必不可少的一项环节。为了增强管线的耐磨性,在管线接口处设置耐磨材料,并制定相关的耐磨设计。其次,管线的维护要制定好相应的保养计划,有专人进行定期的维护保养,为了降低煤线的影响,通常煤线更换周期保持在2h左右。气化炉工况参数如表1所示,气化燃烧炉内的温度会直接影响水冷壁中的水循环管保护层的形成,而直接影响温度的因素便是输送煤粉运量,通过不断的实验,当输煤量达到每小时40t时,产生的热量可使保护层处于一个稳定的状态。
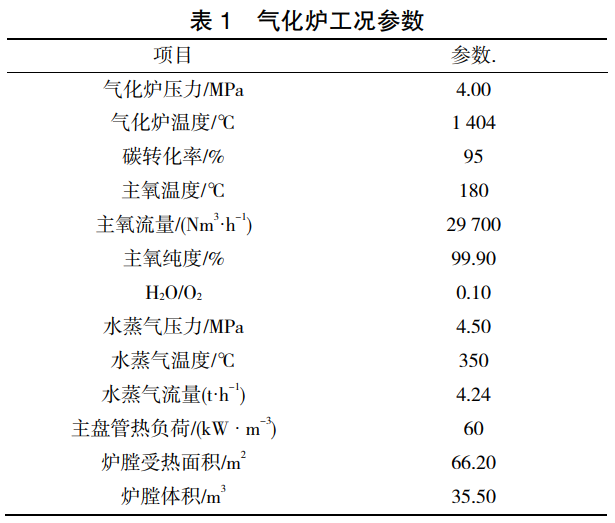
此外,温度控制也是极为重要的一项工作,为了确保炉内温度不超标,通常以炉内甲烷的含量来衡量炉内的燃烧温度。若甲烷质量分数保持在(300~500)×10-6时,炉内温度是较为理想的状态。最后,炉内各部分配件的工作状态也要保持在一个规定的运行状态中,例如,蒸汽网管压力要超过5MPa。汽包中蒸汽含量要逐步减少,保护层形成阶段蒸汽产生量每小时不超过12t,当保护层形成平衡状态后,蒸汽产生量要减少到每小时不超过5t。当渣层逐渐平稳后,循环管内的水流量密度也会随之变化,炉盖水循环管内的密度每平方不超过620kg,主水循环管内的密度每平方不超过550kg。当渣层形成效果较差时,需要及时对气化燃烧炉的炉内温度进行调整,确保保护层处于动态平衡的状态[9]。
3、预防措施
通过上述分析总结,水冷壁冷却效果下降及损坏有如下原因:气化燃烧炉燃烧稳定性差、循环管堵塞或破损导致炉内温度过高、煤粉质量不稳定,气化燃烧炉内热量波动明显。当气化燃烧炉内温度逐渐上升时,燃烧区域内的水冷壁也会受到热量的作用,若局部热量超过渣层的可承受热量范围,渣层平衡状态就会被打破,水冷壁循环管会直接暴露在汽化炉内,当管壁长时间受热时会发生裂缝或爆裂情况;循环管内的水流量不均匀,水流较小、水质不符合吸热标准都会导致冷却效果下降。循环管内部堵塞,给水速度过快或过慢,管内壁水垢过多,循环吸收热量不均也会导致管壁破裂。
1)为了提高循环管材料性质,需采用更高质量的管道材料,例如采用低碳含量的钢材,其原因是低碳钢不容易与氢原子发生反应,所以耐氢腐蚀更好;也可采用细晶粒钢材,其对氢原子敏感性更低,不容易被氢腐蚀;也可采用合金钢材,例如含有稀有金属元素的合金材料,其性能稳定,不与氢原子发生附着反应,抗腐蚀与破裂效果明显;定期进行检查维护,若发现盘管性能下降,需提前更换保养,减少管壁破裂的概率。
2)主煤源性质稳定,通过化学分析来指定某种更为合适的煤源做原材料,若要更换煤源时,需提前对其性质与入炉时间做好精确计算,并控制煤粉的输送含量。此外,关注煤粉燃烧的状态与煤渣的状态,若出现问题,需及时作出调整。
3)提高煤粉输送的稳定性,重点关注送料罐的运行状态,随时检查送料罐内部煤粉的积累情况,减少煤粉成块的概率,保证煤粉输送前的粉末情况。
4)确保整个运送系统的功能,定期对整个系统做检查与维护,做好设备防护工作,避免铁质材料或残渣掉入煤粉设备,检查煤粉输送通道,防止异物堵塞,禁止非工作人员靠近设备,保证煤粉运送畅通无阻。
4、运行注意事项
1)提高循环管内水的质量,制定循环系统水压、流量、水质的标准,减少循环管内水质出现的受热不均问题,以及管道破裂等现象。定期检查循环水系统,避免管道堵塞。
2)对设备进行定期保养与检查,特别是各种压力容器与检测数据仪器。降低生产风险,制定生产规范与设备安全方案,避免重大事故发生。
参考文献:
[1]卫星.航天气化炉的优化措施[J].山西化工,2023,43(2):10-13.
[2]周大平.化工工艺中常见的节能降耗措施[J].辽宁化工,2023,52(3):15-18.
[3]周元祥,沈开俊.航天粉煤加压气化炉的系统优化与控制要点[J].四川化工,2023,26(3):22-25.
[4]张林峰,李西银.稳定航天炉进料系统的探究[J].氮肥与合成气,2023,51(6):66-69.
[5]郑鹏辉.航天炉渣口压差高的原因分析及应对措施[J].煤化工,2022,50(4):82-85.
[6]贺卫.航天炉水冷壁盘管烧损原因分析及预防措施[J].山东化工,2022,51(9):22-25.
[7]张林峰.优化进料系统确保航天炉高效稳定运行[J].化工安全与环境,2022,35(3):70-73.
[8]刘长海.航天炉自动化仪表的使用[J].化学工程与装备,2021(3):45-48.
[9]张洪刚.航天炉粉煤气化装置磨煤系统运行总结[J].氮肥与合成气,2021,49(3):47-50.
相关链接