1、问题的提出
平顶山中盐皓龙盐化有限责任公司有列管式钛换热器4台,按工艺流程分别称为Ⅰ效、Ⅱ效、Ⅲ效、Ⅳ效加热室。每个加热室直径2100mm,内排φ38mm×1.2mm,长6300mm的钛管1399根,与上下管板胀接,换热面积1020m2,换热室的壳程材料为16锰容。在生产中物料走管程循环蒸发浓缩,过热蒸汽进壳程加热。Ⅰ效、Ⅱ效加热室的运行温度分别是143℃和136℃,在运行中,Ⅰ效、Ⅱ效加热室壳程结生磁性氧化铁水垢,颜色黑灰色,管子下段垢的厚度约为6mm,向上依次减薄,质硬而脆,厚度从上到下递增。在下部检查孔处铁垢已经将大约200mm高的空间全部堵塞。铁垢呈现黑灰色,可以被用磁铁吸引。

氧化铁垢的形成原因主要是:锅水中含铁量较高、蒸汽的携带、蒸汽管道停用期间的腐蚀等。经化验表明铁垢的成分主要是磁性氧化铁,约占90%,有少量有机物杂质。结垢影响导热效率或冷却效果,由于这层水垢导热系数比钛材的导热系数小的多,使换热效率大大降低,生产受到一定程度的影响。
结垢使蒸汽通道截面积减少流量降低,污垢粘结在钛表面上促进了垢下腐蚀的形成与发展。所以无论从延长钛设备的使用寿命,还是从提高热传导效率考虑,必须进行清洗[1-2]。
钛材虽然耐腐蚀性相当好,但钛很活泼,能从水中置换出氢。钛之所以耐蚀,是因为其表面生成氧化膜而钝化,而钝化膜一旦被破坏,钛材则极易被腐蚀。在氧化性介质中,钛的耐蚀性良好,而在纯还原性介质中,钛的耐蚀性并不理想。因此对钛换热器的清洗技术要求很高。由于该换热器是制盐生产的关键设备,对清洗质量、工期都有严格要求。但在清洗过程中应避免钛设备的损伤,防止铁污染,防止钛以及同设备的其它部件的腐蚀、电偶腐蚀、缝隙腐蚀以及因腐蚀伴生的吸氢脆化[3]。
采用柠檬酸氨溶液加热可清除铁垢,清洗液需要加热到90℃以上,钛材的导热性极好,清洗过程能源消耗量很多。如果有清洗剂在常温下即可将铁垢清洗彻底且清洗时间又不很长,缓蚀剂能有效防止钛、不锈钢、碳钢的腐蚀,对国内井矿盐行业的节能减排将产生重大影响。
2、清洗剂的筛选
2.1 常用无机酸
对常用的无机酸进行筛选。首先排除了能够腐蚀钛设备的氢氟酸,虽然氢氟酸具有很好的溶解铁垢的能力,但因为氢氟酸可以与钛起配位反应,会形成TIP2-6配位化合物,对钛设备具有强烈的腐蚀性,所以予以排除。盐酸、硫酸、硝酸、磷酸、铬酸等无机酸,都能溶解氧化铁。通过腐蚀试验发现钛材对硝酸、磷酸、铬酸、硝酸+盐酸、硝酸+硫酸具有很好的耐腐蚀性,但溶垢试验发现在常温下硝酸、磷酸、铬酸、硝酸+盐酸、硝酸+硫酸均不能够溶解铁垢,由此可见在高温条件下形成的磁性氧化铁垢具有致密的结构,非常难以溶解。常见的无机酸在常温条件下均难以有效去除铁垢,并且无机酸对换热器的壳程材料具有一定程度的腐蚀性。因此,排除了用无机酸清洗该氧化铁垢的方案。
2.2 常用有机酸
我们希望找到能够与铁离子形成配位化合物的有机酸清洗铁垢,而非以氢离子与铁垢反应。筛选出了乙二胺四乙酸、酒石酸、乙醇酸、柠檬酸、HEDP作为除垢剂,以上有机酸均可以与铁离子形成配位化合物[4-5]。
我们进行了有机酸常温下溶解铁垢的实验。分别用乙二胺四乙酸、酒石酸、乙醇酸、柠檬酸、HEDP配制5%的溶液,加入铁垢,溶解情况见下表1。
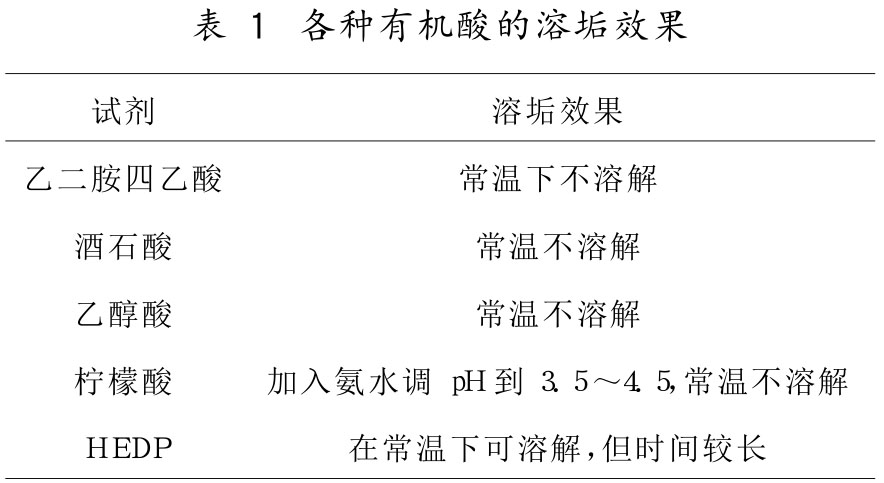
试验表明HEDP能够在常温下溶解铁垢。HEDP产品为无色或淡黄色粘稠液体,密度1.35~1.40kg/L(20℃),具有特异的螯合性能,它能与碱土金属、过渡及稀土元素在广泛的pH范围内形成异常稳定的螯合物。它对Fe3+、Cu2+、Mg2+、Ca2+等金属离子有很好的螯合能力,是一种很好的螯合清洗剂。经毒理试验属低毒,使用十分方便而且安全。它对垢和锈的溶解速率相对要慢些,对金属基体的侵蚀性小,并在清洗后容易钝化,不易产生浮锈等。HEDP与Fe2+的生成配合物的反应如下:
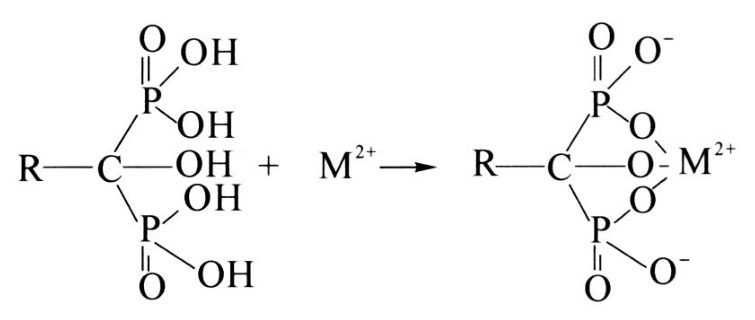
该配合物的稳定常数高达1016.21,反应产物十分稳定,反应的趋势很大[6]。通过筛选,确定HEDP能够溶解这种磁性氧化铁难溶铁垢。
3、HEDP清洗工艺的确定
为了深入研究HEDP的浓度、作用时间、助剂和缓蚀剂对溶垢效率的影响,采用溶垢时间和失重法研究了清洗液溶解铁垢的性能(由于失重质量与时间不成正比关系,所以还采用溶垢时间作为效果指标),并用旋转挂片失重法研究了几组常用的清洗缓蚀剂对HEDP的缓蚀效果,从而为HEDP在钛设备清洗中的应用提供了依据,最大限度地减小清洗过程中所造成的各种危害。
3.1 试验方法
垢样在130℃烘干至恒重,取0.3000g整块垢样进行试验。失重后的垢样用布氏漏斗进行真空抽滤,将残余的垢样放入130℃烘箱烘干至恒重,称重。
旋转挂片实验方法为:将配好的系列溶液放入旋转挂片腐蚀试验仪,安装好试片,调节参数:(25±1)℃、80r/min,并在曝氧条件下运行6h。钛材试片和16锰容试片规格为25mm×20mm×1.2mm[7]。
3.2 结果及讨论
3.2.1 HEDP浓度对溶垢时间的影响
将温度控制在(25±1)℃,取0.3000g整块铁垢试样,投入200mLHEDP溶液中静置浸泡,在HEDP质量分数为2%~6%的几种条件下进行溶垢时间实验,以研究HEDP浓度对溶垢效果的影响,结果如表2。
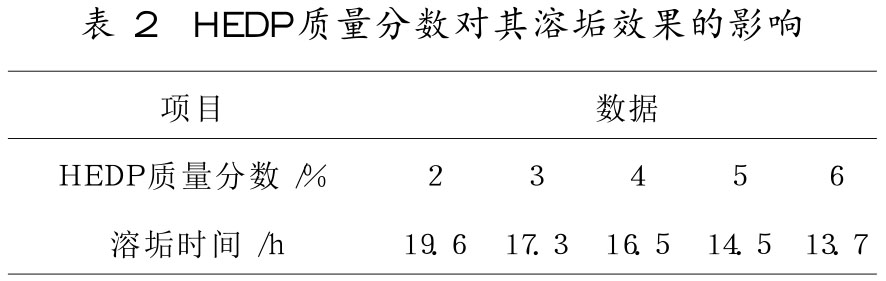
表2表明,HEDP的除垢能力随着浓度的增加而增强。HEDP质量分数大于4%时,其溶垢能力增强幅度加大,因为HEDP作为弱酸,其电离度必随浓度的增加而降低,在质量分数为5.0%时,HEDP溶垢能力的明显增强不是H+起主要作用,而是在较高浓度下,HEDP与铁离子的螯合作用进一步增强的结果。
3.2.2 作用时间的影响
取0.3000g整块铁垢试样置于200mL5%的HEDP溶液中,隔2h测一次垢样失重的质量,结果如表3:
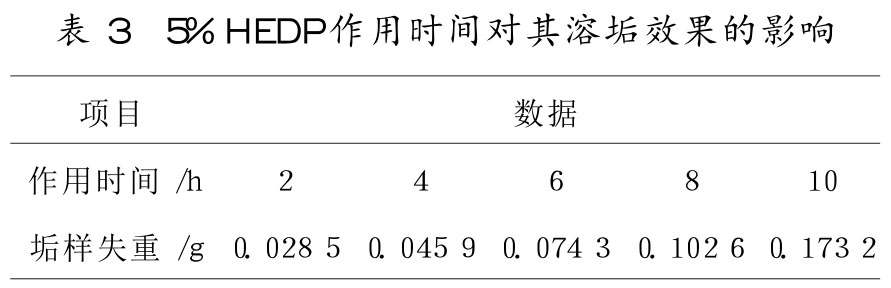
从表3可以看出,在试验时间范围内,铁垢的失重质量逐渐增加,反应时间在6h范围内,失重质量的变化较平缓,反应时间达8h后,失重质量大幅增加。这表明初期HEDP对铁垢的溶解速度较慢,随着时间的延长,HEDP与铁离子螯合反应使铁垢溶解速度大大加快。
3.2.3 助剂质量分数的影响
由于较高浓度的HEDP试剂除垢时间也较长,我们筛选出能够加速溶垢的有机助剂。配制5%的HEDP溶液,加入不同质量的助剂,测其溶解0.3000g整块铁垢所需要的时间,结果如表4。从表4中可以看出,助剂能够加速溶垢速率,溶垢时间随加入量的增加而缩短。但也可以看出,质量分数达到0.8%以后,溶垢时间的缩短效果不明显,因此助剂的添加适量即可。
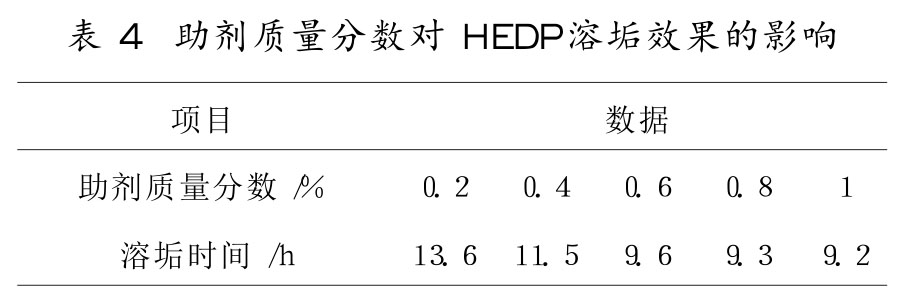
3.2.4 HEDP清洗缓蚀剂的评价
由于换热室内的壳程材料为16锰容,须着重考虑钛的腐蚀与吸氢,及钛、碳钢的电化学反应。取16锰容和钛材试片,按清洗规则要求处理。选取ZB-2、ZB-3、硫脲以及乌洛托品作为酸洗缓蚀剂,进行旋转挂片失重实验,酸洗液配方为5%HEDP+0.6%助剂+0.3%缓蚀剂,结果见表5。
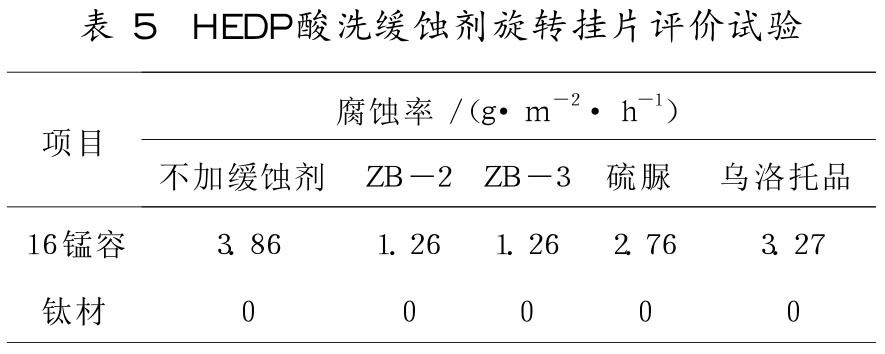
表5表明,HEDP本身作为一种很好的缓蚀剂,对钛材无腐蚀;上述几种酸洗缓蚀剂中,在相同的浓度下以ZB-3对16锰容的缓蚀效果优于其他几种,可极大地减缓HEDP对壳程材料16锰容的腐蚀,可采用ZB-3作为HEDP酸洗的缓蚀剂。
3.2.5 酸洗对于材料硬度的影响
对钛材和16锰容试片分别进行硬度测定后,再投入到质量分数5%HEDP+0.6%助剂+0.3%ZB-3缓蚀剂复配后的酸洗剂中,浸泡10h后再分别测定其硬度,结果如表6所示。
结果表明,复配的酸洗剂对钛材和16锰容的硬度没有影响。
4、生产试验
在实验室工作结束后,我们用最终确定的配方为HEDP5%、助剂0.6%、缓蚀剂0.3%在II效加热室进行工业试验。清洗方案由总师办、科技质量部、生产部会审通过,安排公司检验中心全程化学监督。该设备壳程容积8.6m3,清洗设备安装在0m层1、2号循环泵中间,清洗剂从15m层主蒸汽入口进入加热室,从凝结水出口排出,通过循环管流回配酸槽构成循环回路;钛试片和16锰容试片分别挂在配酸槽内和加热室内主蒸汽入口下3000mm处;清洗过程采用静态与动态相结合的方式,使用杨程50m流量32m3/h的循环泵打循环,累计循环时间在9h左右。
在循环过程用100目不锈钢丝网代分离已剥落的铁垢,清洗14h后打开下检查孔检查,附着在钛管外壁的铁垢已全部清除,总除垢率达98%以上,钛试件和16锰容的腐蚀率都很低,均满足国家标准的要求,达到了预期目的。
5、结束语
1)针对钛换热器上磁性氧化铁垢难以清除的特点,筛选了常见的无机酸和有机酸,通过溶垢试验确定HEDP在常温下能够清除将铁垢,总结了HEDP的溶垢机理,即HEDP是以螯合反应为主的酸洗剂。
2)通过试验进一步确定了HEDP清洗工艺。
HEDP浓度越大,溶垢效率越高;溶垢速率在初期较慢,随着作用时间的增长,除垢速率快速提高;助剂有利于加速溶垢反应;HEDP对钛材无腐蚀,ZB-3缓蚀剂对壳程材料16锰容具良好的保护作用,确定了清洗液相关组分的最佳浓度,并进行了工业试验。在实际操作中,可考虑通过增加HEDP质量分数、延长酸洗时间等措施来提高清洗的效果。
3)加热室磁性氧化铁垢清洗在井矿盐行业有广阔的应用前景。
参考文献
[1]许雅周.一次成功的钛设备化学清洗[J].洗净技术,2004,2(3):54-55.
[2]姬生,孙怡.钛材设备化学清洗工程实践腐蚀与防护[J].腐蚀与防护,2008,9(29):537-539.
[3]郭敏,彭乔.钛的应用开发和腐蚀研究[J].四川化工与腐蚀控制,2000,6(3):28-31.
[4]余存烨.钛设备化学清洗与腐蚀、吸氢[J].化学清洗,1994,4(10):11-19.
[5]周萍.铁垢清洗技术[J].清洗世界,2007,3(23):22-25.
[6]孙纯宾.一次清洗剂HEDP的试验研究[J].山东电力技术,1998,4:20-23.
[7]黄金营,许立铭.HEDP在工业酸洗中的除垢规律及机理[J].石油化工腐蚀与防护,2002,19(1):59-61.
相关链接