钛分离器、钛蒸发器、钛反应釜是三种以钛或钛合金为主要材料制造的工业设备,因其优异的耐腐蚀性和特定功能,广泛应用于化工、制药、海洋等领域。这三种常见的钛设备,所具有性能、制作工艺、应用、选购方法等,腾宇钛业结合多年的钛设备深加工及销售,结合相关资料,浅析如下:
一、各设备特点对比
1、钛分离器
定义:钛分离器是利用物理或化学方法将混合物(气液、液液或固液)中的不同组分进行分离的设备。其核心结构采用钛或钛合金制造,以抵抗强腐蚀性介质(如盐酸、氯离子、高温酸性溶液等)的侵蚀。
性能:耐强酸(如盐酸、硫酸)、耐氯离子腐蚀;分离效率高,适用于气液或液液分离。
材质:工业纯钛(TA1/TA2)或钛合金(TA9/TA10)。
执行标准:GB/T 14845(板式换热器相关)、ASME BPE(卫生级标准)。
制作工艺:焊接采用TIG/等离子焊,内壁抛光至Ra≤0.4μm(制药级)。
应用领域:化工精馏、制药萃取、海水淡化预处理。
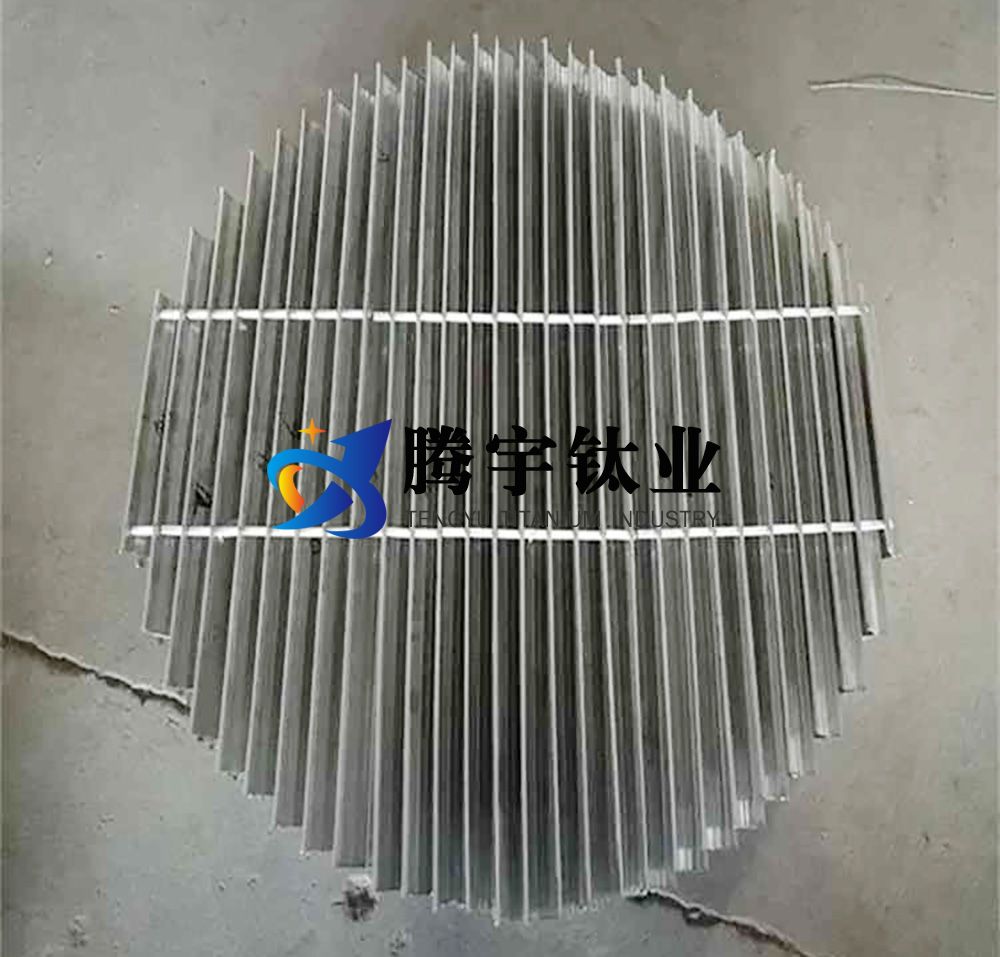
2、钛蒸发器
定义:钛蒸发器是一种通过加热使溶液中的挥发性溶剂蒸发,从而实现溶液浓缩或溶质分离的热交换设备。钛材质使其适用于高腐蚀性、高温介质的蒸发过程。
性能:传热系数高(钛导热性优于不锈钢),抗结垢性强,适用于高温浓缩。
材质:TA2(常规)、TA10(含钼镍,耐高温酸性介质)。
执行标准:GB/T 25151.3-2010(蒸发器专项标准)。
制作工艺:管板胀接+密封焊,多效设计提升能效。
应用领域:盐化工母液浓缩、核废水处理、锂电池材料蒸发。
3、钛反应釜
定义:钛反应釜是一种用于进行化学反应、合成或混合过程的密闭容器,主体由钛或钛合金制成,可耐受强酸、强碱及高温高压环境,并配备搅拌、加热/冷却等辅助系统。
性能:耐压≤6.4MPa,耐温-20~300℃,带变频搅拌(转速可调)。
材质:TA2主体+TA9内衬(局部增强防腐)。
执行标准:GB/T 25151.1-2010(高压反应釜国标)。
制作工艺:整体锻造封头,内壁镜面抛光(电化学抛光)。
应用领域:医药中间体合成、氯化法钛白粉生产、高端染料反应。
二、选购指南
1、关键参数匹配
介质特性:含Cl⁻>500ppm必须选钛;含HF需改用哈氏合金。
温度/压力:超300℃需钛钯合金(TA9);高压工况选锻件结构。
认证要求:ASME认证(出口设备)、GMP认证(制药行业)。
2、工艺优化建议
蒸发器宜选升膜式(高沸点溶液)或降膜式(热敏物料)。
反应釜搅拌器选锚式(高粘度)或涡轮式(高效混合)。
3、供应商评估
查看压力容器A1/A2资质,钛材需提供TA2/TA10材质证书。
案例考察:同类行业成功应用(如氯碱行业蒸发器案例)。
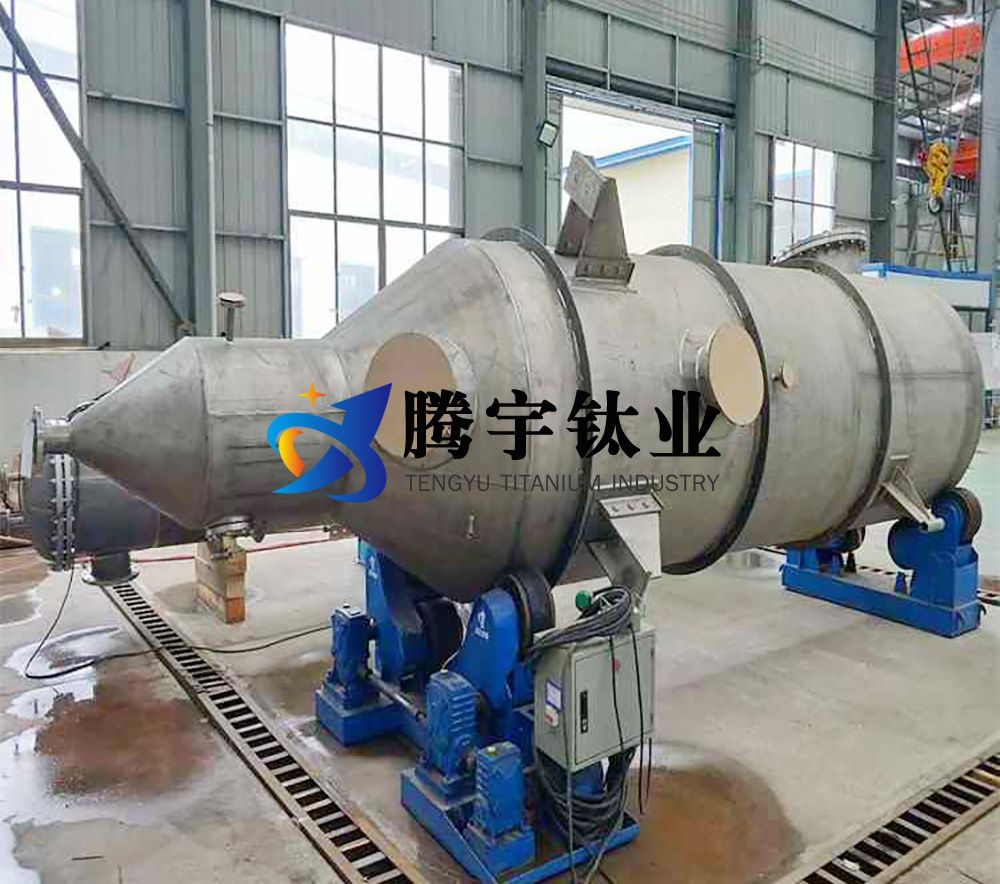
三、使用注意事项
1、防交叉污染
禁止与碳钢工具直接接触(铁离子污染引发点蚀)。
专用吊装工具(尼龙吊带),避免机械损伤。
2、操作规范
升温速率≤50℃/h(防热应力裂纹)。
停机时需用去离子水冲洗(防结晶物残留)。
3、维护要点
每年PT检测焊缝,重点检查气液交界处腐蚀。
密封件更换周期:氟橡胶2年,PTFE 5年(视工况调整)。
四、成本优化策略
复合结构设计:非接触部位采用钛钢复合板(降低成本30%)。
模块化选型:小批量生产选标准型号(交货期缩短50%)。
再生利用:旧设备可通过酸洗(HF+HNO3混合液)恢复性能。
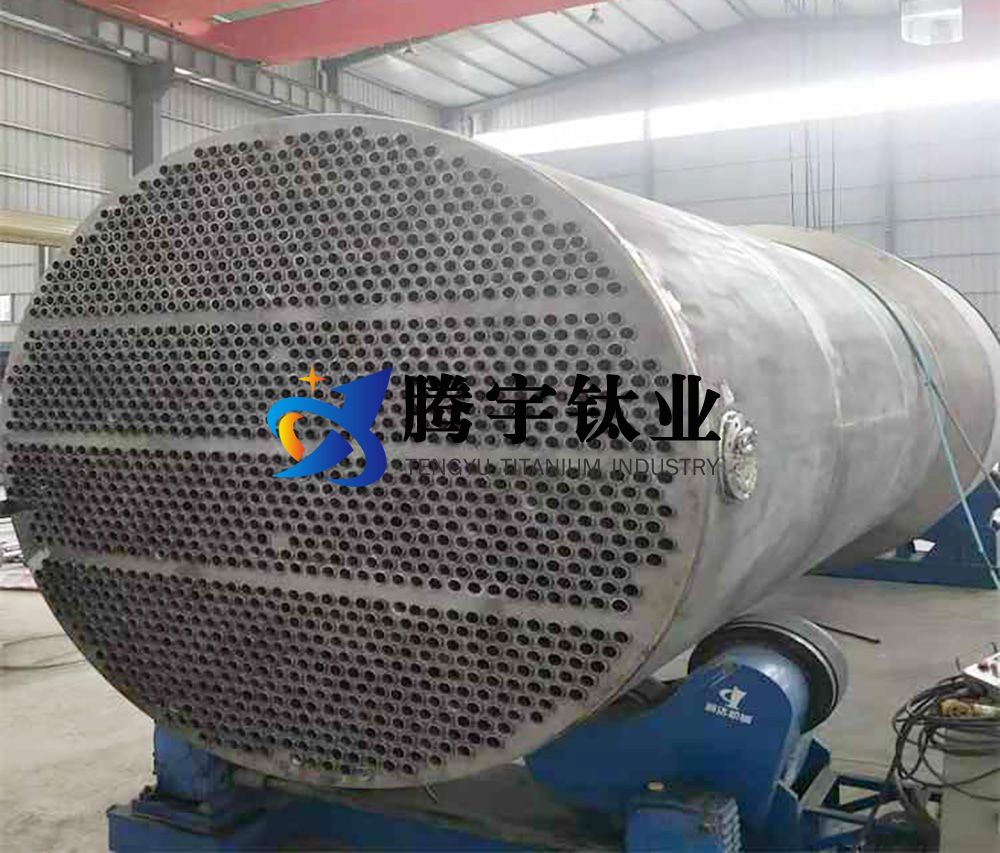
通过精准匹配工况需求与设备特性,可最大限度发挥钛设备的耐腐蚀优势,延长使用寿命至20年以上。建议与具备冶金背景的供应商深度合作,实现全生命周期成本最优。
相关链接