为了实现轻量化目标,进一步提升产品性能,薄壁类零件在航空航天领域得到了日益广泛的应用。由于薄壁类结构的刚度有限,材料去除量大,随之而来的是对零件加工精度与加工效率的巨大挑战。国内外学者主要通过合理分配精加工余量、调节切削参数、刀具参数等,达到控制加工变形,实现薄壁件精密加工的目的。
Liu等针对切削力引起工件弹性变形的误差补偿问题,提出一种基于动态特征的实时变形误差补偿方法,建立动态特征模型,然后根据动态特征模型计算变形量,最终实现了基于功能块的弹性变形加工误差补偿。潘建建立了以平均加工变形量和加工时间为目标、工艺参数为优化变量、期望最低加工精度可靠度为约束的优化模型,并运用直接补偿和迭代补偿法对加工误差进行了补偿,得到了满足预期加工精度的最优工艺参数组合,减小了加工变形量。谭靓等人通过正交试验发现,在一定范围内刀具螺旋角增大,会引起轴向力增大,导致切削振动加剧,切削过程不稳定,从而使表面粗糙度增大。邓亚弟等通过单因素对比试验法得出随着刀具螺旋角的增加,刀具与工件的接触刃长度增加,轴向力Fz 较Fx 、Fy 增大更加明显。田汝坤通过刀具结构对腹板变形影响极差分析得出结论,刀具螺旋角越大,薄壁腹板变形越大,故加工腹板时应该选用小螺旋角立铣刀。张攀、陈蔚芳提出利用变铣削厚度方法,通过有限元分析,得到恒定切削参数下的让刀量,再通过切削参数、切削力和让刀量迭代计算获得需补偿量,从而得到相对欠切量最小的走刀轨迹。
综合现有研究现状,国内外学者围绕薄壁件加工变形问题相继研究了许多控制方法,但仍有很多问题有待进一步完善。目前的研究多是以框类、梁类等弱刚性零件位为研究对象,研究对象单一、结构形式简单,研究成果不具有通用性,不适用于本文中钛合金超薄壁板的加工。
从现有参考文献可知刀具的螺旋角对薄壁件的加工有重要影响,在一定范围内,螺旋角越小薄壁件变形越小,但对于螺旋角为0°的直刃型立铣刀研究较少。本文对直刃型铣刀进行展开研究,经过测试发现,螺旋型立铣刀加工时Fz 在正负双向间往复,对腹板产生“上拉——下压”的循环作用。而直刃型立铣刀(螺旋角为0°)的Fz 则在正向(垂直工作台指向地面为正向) 区间内波动,一直下压钛合金板材。真空吸盘的吸附效果受到负压大小、吸盘直径、密封条布置位置和壁板底面粗糙度、面积等内外部因素影响,具有不确定性。相较之下,在采用真空吸盘的基础上,使用直刃型立铣刀更有助于腹板的精密加工,可有效避免吸附力不足导致的腹板过切。
考虑径向切深对侧壁变形的影响机制,在较大径向切深条件下,同样的加工余量走刀次数减少,工件在切削过程中残余刚度相对较大;继续增加径向切深,虽然工件残余刚度提高,但是切削力也进一步增大,对刀具的寿命也有较大影响,两个因素综合影响时,切削力成为主要影响因素。故而设计合适的精加工余量成为抑制侧壁变形的有效方法。
本文根据该钛合金超薄壁板零件的特点,针对试加工中发生的腹板过切、侧壁欠切的问题,对相关原因进行了分析研究,采用不同于常规的螺旋型立铣刀的直刃型铣刀进行加工研究。提出了用直刃型立铣刀加工薄壁腹板,精密设计侧壁精加工余量的钛合金壁板精密高效加工工艺方案。通过实际加工验证了该方案能够保证零件加工精度、提升加工效率,有力推动了产品的批产工作。
1、钛合金超薄壁板的结构
钛合金超薄壁板的结构如图1所示,其主体结构为1mm厚的腹板,平面尺寸跨度较大,长760mm,宽 290mm,腹板上带有多边形型腔结构,型腔侧壁的壁厚为0.5mm,高度为3.5mm,型腔内部的腹板厚度仅为0.5mm,侧壁结构的厚度/高度比为1/7,腹板的厚度/ 侧壁高度比也为1/7,属于典型的弱刚度结构。超薄壁板的毛坯为5mm厚钛合金板材,材料去除率达到了 92.6%。
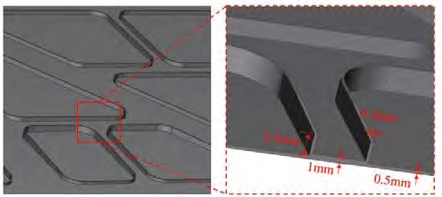
图1 超薄壁板零件结构示意图
2、薄壁壁板加工的难点分析
2.1 薄壁腹板过切现象
真空吸盘的吸附效果受到负压大小、吸盘直径、密封条布置位置和壁板底面粗糙度、面积等内外部因素影响,具有不确定性。在试验加工中,钛合金板材由压板压紧边缘同时使用真空吸盘吸附,使用常规的螺旋型立铣刀加工型腔内腹板,频繁发生腹板局部过切甚至被过切的问题,严重影响了零件的加工精度与成品率。
从真空吸附实况和刀具切削力试验出发对这一问题进行了分析。零件腹板为薄壁,同时采用螺旋型立铣刀进行切削,此时根据实际测量切削力Fx 、Fy 、Fz 进 行分析,工件受到的Fz 正负交替,当工件的表层受到负向(垂直工作台指向地面为正向)Fz 的作用,形成向上的牵引效果,同时与真空吸附力发生对抗,当刀具行至转角处时,切削量增大,Fz 增加至大于真空吸附力时,被加工表面加工中被去除的材料厚度4.5mm,而腹板仅有0.5mm的厚度由于腹板厚度尺寸较小,刚度弱,极易发生过切撕裂。如图2所示。
2.2 侧壁加工欠切问题
壁板内型面的型腔侧壁厚度0.5mm,高度3.5mm, 厚度/高度比达到了1/7,属于典型的薄壁结构,在试加工中发现侧壁厚度超差,即所谓的欠切问题。由于侧壁的刚度弱,在加工中受到切削力的作用发生弹性变形,薄壁顶部的弹性变形大于根部的弹性变形,因此加工后的薄壁结构往往顶部壁厚偏大,而根部壁厚则能满足精度要求,如图3所示。
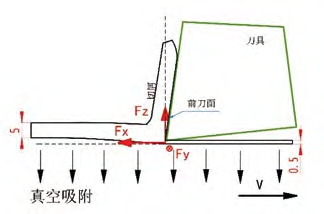
图2 腹板过切机理
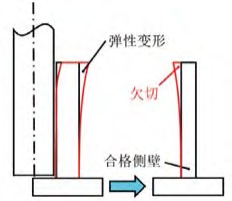
图3 薄壁加工的弹性变形
3、试验
3.1 试验方案
3.1.1 直刃型立铣刀加工腹板
根据上述分析,提出采用直刃型立铣刀控制轴向切削力方向的方法以避免腹板的过切。与常用的螺旋型立铣刀不同,直刃型立铣刀的螺旋角为0°。为了验证所设计的直刃型立铣刀的切削力方向,使用螺旋型立铣刀与新设计的直刃型立铣刀(见图4)对TA15 钛合金板材进行切削试验,在相同切削参数下测量并对比两种刀具的切削力。试验用的两种铣刀均由刀具提供,刀具的硬质合金材质、涂层等均相同,铣刀的结构参数列于表1。
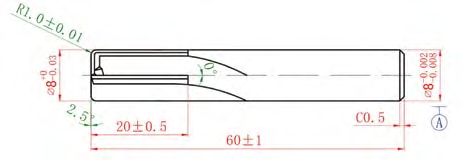
图4 D8R1直刃型立铣刀的结构
表1 切削力对比试验使用的两种刀具
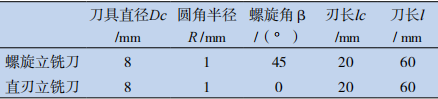
切削试验在三坐标加工中心上进行,切削参数见表2。使用压电测力仪及其配套的测量系统测量切削力。Fx 为进给方向切削力,Fy 为切宽方向切削力。轴向切削力Fz 以垂直工作台指向地面为正向,即被加工材料受到向下的压力,负向则相反。
表2 切削力对比试验的切削参数

3.1.2 设计侧壁加工余量
针对薄壁加工的弹性变形问题,工艺方案从利用零件自身结构刚度的角度出发,通过预留足够余量的方法提高薄壁结构的加工精度。为薄壁的精加工预留足够的余量后,在加工过程中可以利用未加工部分的刚度作为对薄壁的辅助支撑,以此抑制侧壁弹性变形导致的欠切问题。
试验设置4种精加工余量(0.5,1,1.5, 2mm)进行分析。在侧壁精加工中,预留的余量将被一次性切除到位,因而试验中切宽的尺寸即是精加工余量的尺寸。仿真中对应各加工余量而加载的切削力由切削试验直接测得,试验使用D8R1直刃型立铣刀切削TA15钛合金板材。试验的各项切削参数见表3。
表3 不同精加工余量的切削力试验参数
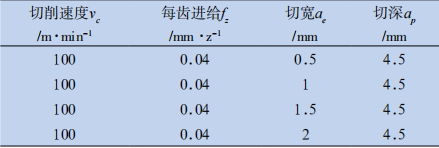
3.2 试验结果
3.2.1 直刃型立铣刀与螺旋型立铣刀切削力对比
对比试验结果:螺旋型立铣刀与直刃型立铣刀两者的切削力的变化分别如图5(a) 与(b)所示。螺旋型立铣刀的Fz在正负双向间往复,而直刃型立铣刀的Fz 则在正向区间内波动。由此可以验证对壁板腹板过切原因的推测。当使用螺旋型立铣刀面铣腹板时,由于腹板厚度仅为0.5mm,Fz 上下往复对腹板产生“上拉——下压”的循环作用,一旦板材局部厚度不均匀存在翘曲凸起,刀刃切入后将发生过切的问题。而使用直刃型立铣刀切削时Fz 则一直下压钛合金板材,因此可以避免腹板过切。此外,还可以发现在试验参数下直刃型立铣刀的切削力相对螺旋型立铣刀的更小,能够降低切削过程中产生的残余应力。因此,直刃型立铣刀适合薄腹板加工。
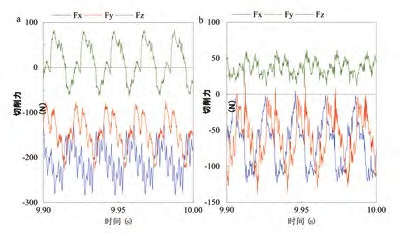
(a) 螺旋铣刀的切削力 (b) 直刃铣刀的切削力
图5 两种刀具切削力变化
3.2.2 不同侧壁精加工余量设计试验结果 设
置4种精加工余量(0.5,1,1.5, 2mm)进行试验测得的切削力如图6所示,其中Fy 为切宽方向(垂直于侧壁)的切削力。在相同条件下,预留更多的精加工余量使得Fy 逐步增加,同时预留更多余量时,前序切削产生的残余应力更小,更有利于精加工时切削。
将测得的切削力输入有限元分析算例,对不同余量下的侧壁结构在切削力作用下的变形进行分析。有限元分析软件是Abaqus,杨氏模量为1.18e5MPa,密度 为4.45e-9t/mm3 ,泊松比为0.39。4组余量的侧壁的最大法向变形仿真结果如图7所示,较大余量对应的侧壁法向最大变形量相对更小。相比试加工中应用的0.5mm余量,设置较大的余量能够增强加工中的侧壁刚度,对抑制侧壁的壁厚超差有显著的帮助。根据切削力试验的结果,考虑到直径D8的刀具切削载荷不宜过大, 因此侧壁的精加工余量(即精加工的切宽)也不应一 味增大。参考仿真结果,当精加工余量大于等于1mm 时,最大变形少于0.05mm,即加工的百分比误差小于 10%,处于精度范围内,因此设置侧壁精加工余量为 1.5mm,实现侧壁的精密加工。
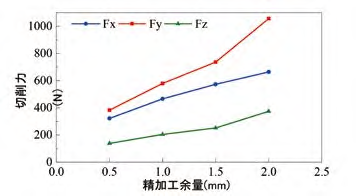
图6 4种切宽的切削力
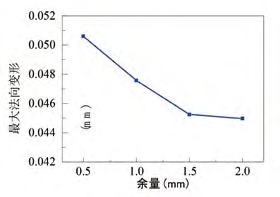
图7 不同余量侧壁最大法向变 形仿真结果
4、试验结果应用
将上述试验结果应用至钛合金超薄壁板腹板和侧壁加工中,在解决了技术问题的基础上,试加工过程稳定,因此增大腹板切削参数,切宽不变,进给速度从原本100mm/min提升至175mm/min,提升加工效率75%。加工出成品零件如图8,对零件的侧壁厚度尺寸进行检测,其侧壁厚度理论尺寸0.5mm,设计要求尺寸误差 ±0.05mm,合格尺寸范围应在0.45~0.55mm之间,实测尺寸为0.5~0.547mm,仅占给定公差带47%,如图9所示。对腹板进行取点测量,测量结果如图10所示,设计要求尺寸误差0.5±0.05mm,测量尺寸0.46~0.539mm,占公差带79%,表面粗糙度达到Ra1.6μm,满足设计要求。
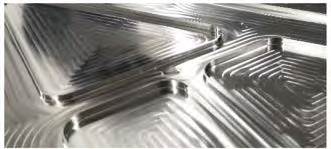
图8 加工后的壁板
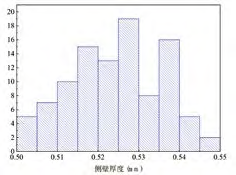
图9 侧壁厚度实测值分布图
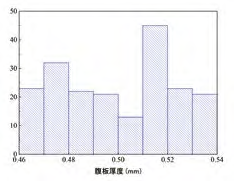
图10 腹板厚度实测值分布图
5、结论
本文针对钛合金超薄壁板的加工难点问题进行了分析与试验验证,主要的工作有:
① 通过对直刃型立铣刀与螺旋型立铣刀的轴向切削力的差异进行了分析与试验验证,提出使用直刃型立铣刀进行精密加工工艺方案。利用直刃型立铣刀向下的轴向切削力避免腹板的过切,并且辅助压紧零件。
② 利用余量加强刚度结构在加工中的刚度,结合切削试验与有限元仿真,获得适当的精加工余量。
③ 基于上述技术要点设计了钛合金超薄壁板的精密加工工艺方案,在实际生产中取得了优秀的结果,零件腹板和侧壁尺寸满足设计需求±0.05mm公差范围,零件粗糙度可达Ra1.6μm,满足设计要求。以上工作为航空航天领域整体薄壁腹板类零件的加工提供了有益借鉴。
相关链接